Microsoft Azureコラム
Writer:佐藤翔
IoT/AIで装置の故障予知。メリットと実現までの流れをざっくりご紹介
製造現場では、ラインの停止による稼働率低下は最小限に抑えたいところです。
そのため、IoTによる装置の故障予知が普及しています。故障の自動検知や故障を事前に予測して未然に防ぐことが可能になりました。IoT/AIによって温度、湿度、振動等のデータを常時取得して正常な稼働状態を定義し、正常時と異なる兆候が現れたら故障の兆候と判断して通知をします。これにより未然の修理対応が可能になり、コスト削減や人員不足解消を実現しています。IoT/AIを積極的に現場に取り入れていきましょう。
また、故障予知を販売製品の付加価値として提供することで、新たなビジネスとして収益拡大にもつながります。
ネクストステップにおすすめ
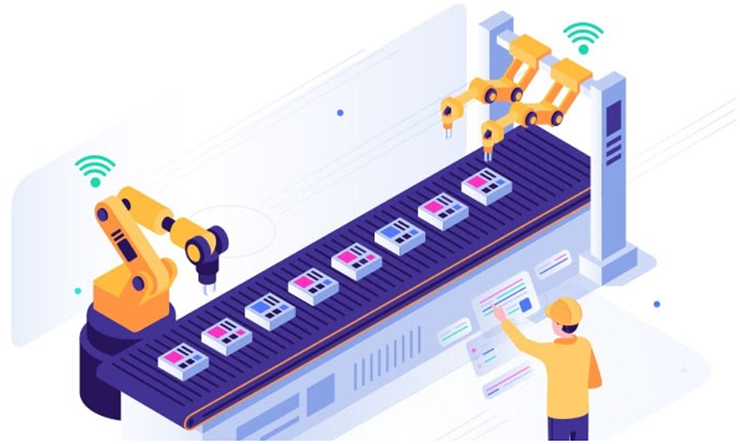
IoT/AIによる故障予知のメリット
- ダウンタイムを最小限に抑えて生産性を向上
- 故障予知を新たな付加価値サービスに
この2つが大きなメリットです。課題とセットでひとつひとつ見ていきましょう。
1. ダウンタイムを最小限に抑えて生産性を向上
課題:
故障発生!でも不具合の原因を特定に時間がかかるしリソースも割けない...
解決:
AIで故障箇所を早期に特定し、生産性の向上を実現!
IoTによって集めたデータをAIで解析することで、故障の可能性が高い箇所を早期に特定できるので、ダウンタイムを最小限に抑えられます。
また、原因特定の調査に熟練作業員のリソースを取られず製造作業に専念することが可能です。その結果、生産性の大幅な向上が期待できます。
故障が発生しやすい原因の分析によって、製造品質をさらに向上!
機械学習により故障が発生しやすい状況が解析できるようになり、より優れた稼働条件への最適化が図れるようになり、製造品質の向上につながります。
2. 故障予知を新たな付加価値サービスに
課題:
価格競争から脱却し、利益率を上げたい...
解決:
故障予知をサービス化することで強力な付加価値を実現!
工場内で稼働する装置の故障を未然に防ぎ、継続的に安定稼働を実現できるようになれば、稼働率の最大化を目指す企業の満足度も向上します。「故障予知」を付加価値サービスとして提供することで、新しいビジネスの展開が可能となります。
装置の故障予知、2つの事例
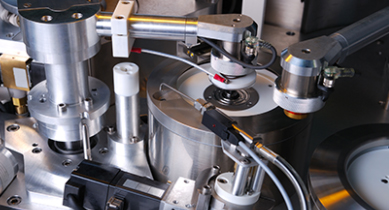
製造装置の保守コストを削減
製造装置の稼働時間が増えると振動や部品の劣化によって故障の可能性が高まるため、基準値に到達すると、使える状態でも部品交換をするケースがあります。また、使用環境によっては基準値に達する前に故障が発生してしまうこともあります。IoT/AIにより「故障が起こりそう」なときにのみ対応ができるようになり、予期せぬ事態に備えた定期点検や在庫の確保などの保守コストを削減できます。
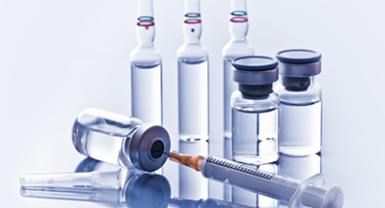
業務停止を未然に防ぎ、経済的損失を減少
産業用の冷蔵庫や薬品保管庫など、故障で稼働が停止すると業務に影響を及ぼすだけでなく、衛生管理上の問題から在庫破棄などの大幅なコストが発生します。故障予知により停止のリスクを大幅に削減することができ、経済的損失を防げます。
また装置の付加価値として故障予知サービスを提供すれば、利用する側も安心でき、顧客満足度の向上につながります。
装置の故障予知、実現までの流れ
装置の故障予知の実現には、下記の流れで進むのが一般的です。
STEP2の条件定義までの期間の目安は、2週間〜1ヶ月です。
STEP1 目的の確認
対象機器と取得できるデータを整理します。
STEP2 条件定義
下記を定義します。
- 取得するデータの種類(温度、湿度、振動、傾きなど)
- データ取得方法(センサー、カメラなど)
- データ取得環境(定期取得、常時取得など)
- 故障の判断基準の定義
STEP3 サービス選定
Azureのどの機能をどう使うか、システム構成の検討をします。
STEP4 システム構築
システム構築の実施
東京エレクトロンデバイスでは、ご紹介したような事例で利用できる各種ソリューションを販売しています。
こちらでも詳しく紹介していますので、ぜひご覧ください。
東京エレクトロンデバイス データ分析(故障予知)ソリューション一覧