Microsoft Azureコラム
Writer:手戸 蒼唯(てど あおい)
スマート工場とは何か、工場へのIoT導入でできること
昨今、「スマート工場(スマートファクトリー)」が注目を集めています。スマート工場とは、複数の工場設備にさまざまなセンサーやコントローラを設置し、取得したデータをネットワーク上で常時監視、分析することにより生産性や品質を向上させる工場のことです。
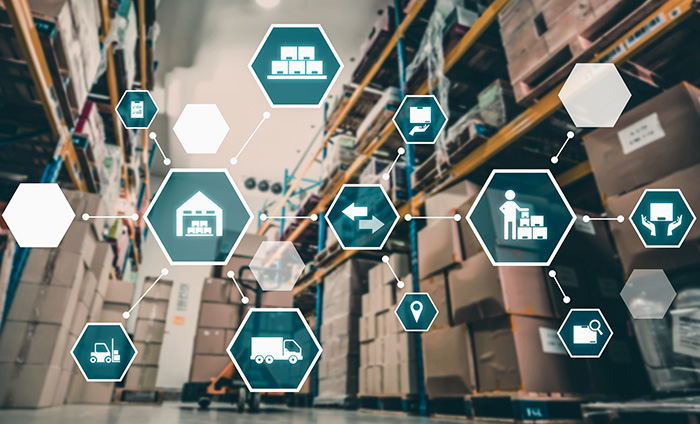
スマート工場、スマートファクトリーとは
製造業で注目されている「スマート工場」とは?
スマート工場とは、理想的には、さまざまなセンサーを設置した生産設備と工場全体の基幹システムをインターネットなどのネットワークによって接続し、管理することによって生産性や製品品質を高めた工場のことをいいます。
スマート工場では各設備の稼働状況、稼働率、エネルギー使用量、ユーティリティ使用量、作業員の行動状況など、センサーで取得できるさまざまなものが「見える化」されており、それらが中央監視室などのブラウザ上で一元管理されています。
取得したデータを分析することで、設備の稼働時間の最大化、故障時間の最小化、労働環境の最適化などの改善が期待できます。さらにその対策の結果から、新たな改善策を検討することも可能です。
近ごろでは、各設備や作業員の行動などから得られた膨大なビッグデータの分析にAI技術を活用し、設備の故障を検知したり、熟練技能者の行動をマニュアル化するなどといったソフトウェアの開発も進められています。
製造業の抱える課題を解消する一つの手段として期待されています。
スマート工場を巡る動向
世界では、製造業にIT技術を導入し改革を進める「インダストリー4.0」を背景に、スマート工場化が進んでいます。日本でも2016年、政府により「Society 5.0(サイバー空間とフィジカル空間を行動に融合させ、経済発展と社会課題の解決を図る)」という社会概念が提唱され、同様の動きが加速しています。
日本における既設工場のスマート工場化には次のような課題があるといわれています。
- 一つの製造に特化した産業ロボットが導入されている
- スマート工場化の費用対効果がわかりにくく投資判断がしにくい
- 適切なネットワークの構築までのハードルが高い
- データを活用するための仕組みづくりに関するノウハウがない
- セキュリティ問題により情報漏洩のリスクがある
一方で、スマート工場化は日本の製造業と相性が良い面もあります。
わかりやすい例として、スマート工場という概念の発祥であるドイツの製造業をみてみましょう。ドイツでは社員数500人以下の中堅・中小企業が全体の約8割を占め、その多くは大企業の製品の工程のひとつを受け持っています。実はこの産業構造は、日本と非常に似ているのです。
そのドイツでは、スマート工場化によって各企業間で生産ラインの共有化などの連携をすすめ、企業の枠を越えた全体最適化に取り組んでいます。
こういった成功例を踏まえると、日本の製造業においても同様に、製品の品質向上や安定供給の観点からスマート工場化が進められていくと考えられます。
スマート工場とIoTの関係
スマート工場を構築するためにはIoTの技術が不可欠です。ここではIoTについて紹介します。
IoTとは
IoTとは「Internet of things」の略で、設備や家電製品などのモノをインターネット上で接続する「モノのインターネット」を意味する言葉です。
IoTによって、例えば製造業などの工業分野では、設備状況をリアルタイムに監視したり、遠隔での制御などを実現できます。またデータをもとにした改善策の検討や、AIと組み合わせた生産工程の効率化や故障予知なども行えるようになります。
さらに近年では、工業分野だけでなく家庭やオフィス、商業施設などで多く取り入れられています。
工場にIoTを導入するとできること3つ
工場にIoTを導入することで次のようなことが実現できます。
生産ラインの見える化
各設備のセンサーからデータを収集し、常時監視を行うことで設備の稼働状況、稼働時間、停止時間を見える化できます。これにより、現状の工場の稼働率や生産性が数値でわかります。
多くの工場で課題としてあげられる生産性の向上ですが、まず、現状の生産性を正しく把握することで適切な対策が検討できるようになります。
また、電流値や振動値など設備状態を判断するための指標を見える化することで、経年劣化などの傾向を監視でき、故障が発生する前に設備を補修する予知保全が可能となります。
昨今では、正常稼働時に収集したデータを教師データとしてAIに学習させ、異常な傾向が現れれば検知し、人間が気づく前にアラートを発報するなどのソフトウェアも開発されています。
省エネ化の実現
各設備の電力や熱などのエネルギー使用量を見える化し、比較することで設備、生産品種ごとのエネルギー原単位や生産量に依存した変動エネルギー、生産量に依存しない固定エネルギーの割合などを算出できます。
これらの値を傾向監視することで、閉止バルブの劣化による蒸気や圧縮空気の漏れや待機電力など、設備が停止している間にも発生しているエネルギーロスがわかり、対策を講じることで省エネ化が実現できます。
また、エネルギー使用量が見える化されていることで対策実施後の効果測定も容易になり、ほかの工場や生産ラインへの横展開も実施しやすくなります。
省エネ化を目的として既存の設備にセンサーを設置する場合は、投資採算性を考慮し、エネルギー使用量の多い設備に優先的に導入して、一定の効果が得られれば横展開を進めるというアプローチが一般的です。
設備の自動制御化
最新の設備では、従来は人間の手入力によって実施されていた生産状況ごとの制御システムのパラメータ設定変更をAIが自動で行うという事例も出てきています。
最適なパラメータ設定を見出すためには、一つずつ値を変更させながら結果をみて修正するという試行錯誤が必要なため、これらを自動化することで生産ラインの 人員コスト削減につなげられます。
このような取り組みも一度にすべての設備を自動化することは難しく、まずは小規模でシステムを導入し、意図的に異常状態を作りだすなどの疑似的なトラブル検証などを重ね、問題がなければ展開していくことが重要です。
スマート工場化を進めるIoT導入3つのフェーズ
従来の工場をスマート工場化させるためには次の3つのフェーズが必要です。
(1)見える化
最初に行うべきことは設備の稼働状況の「見える化」です。 設備から取得できるデータとして、稼働状況、温度、電流値、振動値、水や圧縮空気などの使用量などさまざまなものがありますが、それらのデータを見える化することで、現状を正しく把握できます。
例えば、従来の方法では生産工程の中で稼働率を低下させる要因である箇所がわかりづらく、投資すべき設備がわからない場合でも、工場全体の状況を俯瞰的に見える化し、分析することで、適切な投資判断が可能となります。
(2)稼働状況の確認
工場全体の見える化が実施できたら、次は各設備の稼働状況を確認します。
全体の稼働率はどの程度か、各設備の稼働率との乖離はどの程度か、工場全体で稼働率が下がる要因となるラインはどこか、その原因は何かなど、数値を比較することであらゆる仮説を立てることができます。
一見、常時稼働しており、稼働率が高いように考えていた設備でも、実際に数値化すると管理者が把握できていない一時停止が多く、稼働率が低いという場合もあります。データを取ることで初めて正確な稼働率がわかり、潜在的な工場の問題を顕在化できます。
(3)省力化
設備からのデータが収集できたら、そのデータをもとに稼働率を低下させる要因となっている工程の一部自動化などが検討できます。
また、費用対効果が見合えば、 AI技術などを利用して人の動きを分析し、工作機械に置き換えることで一つのラインの全自動化も検討が可能となります。
IoTは常に発展し続けている技術であり、変化に対応していく必要がありますが、まずはIoTの基盤となる現場のデータを「見える化」し、ビッグデータを収集することから始めてみましょう。
IoTによるスマート工場化を図るメリット
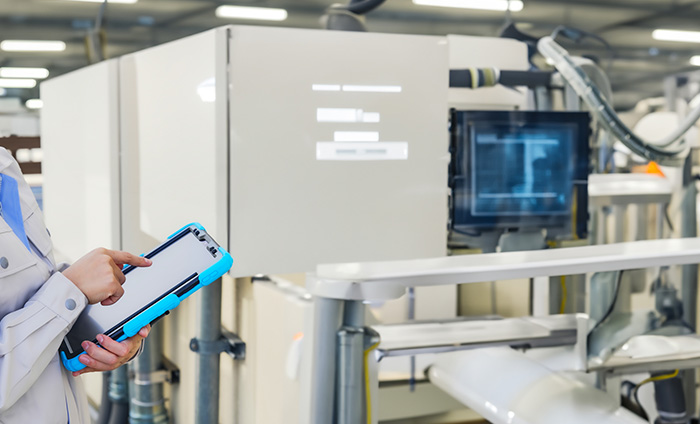
IoTによりスマート工場化を行うことで次のようなメリットが期待できます。
複数の工場間で柔軟な対応が可能に
複数の工場がスマート工場化しシステムで連携できれば、トラブル発生時などにリアルタイムでの柔軟な対応が可能となります。
例えばある工場でトラブルが発生したとしても、即座にトラブルを感知して、別の工場でその分の製造をカバーするといった対応ができます。
従来の工場では同工場内でのラインの組み換えは可能でしたが、複数の工場で連携をとることで、さらなる安定供給が期待できるようになります。
また、工場同士の情報共有システムを確立することで、在庫や予備品の状況なども複数の工場で共有化でき、在庫の数を減らすなどの対策も実施できるようになります。
物流サービスの発展もあり、今後は距離の離れた工場でのリアルタイムな連携が全体最適化を図るうえで非常に重要です。
人員配置を最適化できる
スマート工場で蓄積されるデータにより、従業員の生産能力の数値化なども可能となります。収集したデータから、技術力の高い従業員とほかの従業員の違いを分析し、技術やノウハウをマニュアル化することで、従業員全体の技術力向上につながります。
近年、製造業では、定年退職による熟練者の一斉引退により製品品質の担保が厳しくなるという問題がおこっています。熟練者の経験知をIoTにより形式知に変換することで、技術や技能を伝承していくことで、人に依存しない品質の確保が可能となります。
異常や故障などを早期に発見する
日々のデータを蓄積して傾向を分析できていれば、異常があった場合には即座に感知し、トラブルの予兆を早期に発見できます。これにより、故障が発生したあとの事後保全から、故障前に補修する予知保全へ移行できるようになり、設備の突発停止リスクを低減できます。
また、昨今では感染症などの対策として一時的に現場作業者が出勤できず、工場が操業停止に追い込まれるケースなどが発生しました。このことから、現場作業者がいなくても生産設備を遠隔保全する仕組みを導入するといったスマート工場化に取り組む企業が増えてきています。
モニタリングによる予防保全にとどまらず、感染症など事業の継続にかかわるような大規模災害への対策としても、「スマート工場化」という選択肢に注目が集まっています。
スマートファクトリーの導入事例
ここではスマート工場の導入事例を紹介します。
事例1:エネルギー使用量の見える化
工場のIoT化の事例としてもっともよくあげられるのが、エネルギー使用量の見える化です。工場では、電力、蒸気、水、圧縮空気、ガスなどのさまざまなユーティリティが利用されていますが、これらの使用量を設備ごとに見える化することで、ラインごとのエネルギー削減計画などの策定が可能となります。
エネルギー使用量の見える化は、目先の省エネ対策と比較すると効果が出るまでの期間が長く かかり、効果測定がしにくい領域ではありますが、長期間の傾向を監視することで初めて分析が可能となるため、工場を新設する場合は、建設当初から必要経費として考慮しておくことをおすすめします。
事例2:生産設備の異常・故障監視
無人の生産設備では、各設備の生産中に異常や故障が発生した場合、設備上部に取り付けられた信号灯が点灯して、設備管理者に通知するという現場がよくみられます。この方式で素早いトラブル対応を行うためには定期的な現場巡回や管理室から監視カメラでの常時監視が必要です。
この問題を解消するために、スマート工場化を行い、異常発生時の信号灯の点灯に利用されている接点信号をデジタル信号に変換。無線で管理室に飛ばすことで、常時監視が不要となり、設備の停止時間を最小化したという事例があります。
また、設備名、発生日時などを正しく記録できるので、各設備の異常発生頻度から設備更新が必要な箇所も容易に特定が可能となります。また、人による記録作業も自動化できるため、業務効率化にもつながります。
事例3:製造工程の見える化により生産ロスを大きく削減
大手電気機器メーカーの事例 では、経済産業省の委託を受け、スマート工場実証事業が行われています。ネットワークカメラやセンサーデバイスなどを工場内の生産設備に設置し、インターネットで接続して、生産ラインのIoT化を進め、収集したデータをAIで分析して非効率的な作業や工程を発見することにより、生産ロスを大きく削減できることが実証されています。
IoTを全面的に導入するためには多額のコストがかかる場合が多いため 、今後も国の予算なども使用しながら費用対効果を検証していく流れが進むと考えられています。
事例4:熟練技術者の技術伝承に成功
人手不足の製造業では経営課題の一つとして熟練者の技術伝承、技能伝承があります。これまで長年の経験や勘により支えられてきた品質が、熟練者の引退により失われる可能性があるため、引退を迎える前に、熟練者の経験知を形式知化する必要があります。
また、海外進出を考えた場合、現地のスタッフを育成し、国内と同様の品質を維持するためには言語の壁がある中、国内の熟練者の技術や技能をマニュアル化し、正しく教育することが重要です。
大手総合空調メーカーの事例では、スマート工場化に取り組み、国内の熟練職人の動きを動画で撮影。それをAIで計測、解析、複数の評価項目で評価する仕組みを構築し、それらを現地スタッフの教材として利用することで技能伝承を効率化し、海外の多数の拠点へ展開しました。これにより、新しく入った従業員は、経験値、言語にわらず一定の技術力を身に着けられる仕組みを構築しています。
スマートファクトリー化の第一歩としてIoTセンシング技術を導入するなら
工場をスマート工場化させるために重要な第一歩はセンシング技術の導入による「見える化」です。
工場環境を「まずは見える化」したい方において失敗しないためには、導入によって達成したい課題を明確にし、過剰仕様にならないよう注意しながら、適切な機器やパッケージ化されたソフトウェアを利用し、可能な限りコストを抑えながらスモールスタートさせることが重要です。
これらの課題を解決するサービスとして、東京エレクトロンデバイスがご提供している「IoT INSIGHT CaaS」では月額3,000円から利用可能で、開発なしでスモールスタートさせることができます。
また実際の導入後に開発が必要な場合は、専門のエンジニアが対応することも可能です。IoT化を推進したいがどんなことができるのかわからない、最小限の投資でまずは試してみたいという方はぜひ東京エレクトロンデバイスにご相談ください。