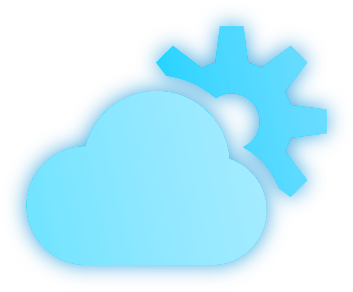

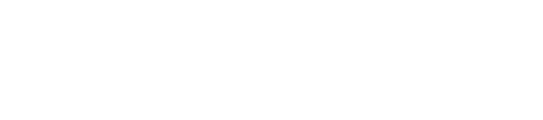


Writer:手戸 蒼唯(てど あおい)
製造業のための設計DX導入ガイド:Azureで実現する競争力向上戦略
現代の製造業は競争の激化、市場ニーズの急速な変化、技術革新の加速などにより、さまざまな課題に直面しています。特に開発期間の短縮、コスト削減、製品品質の向上が急務となっています。これらの課題に対応する一つとして、「設計DXの導入」があります。
本記事では、設計DXの基本概念から具体的な適用例、AIやクラウド技術の活用法まで、製造業のDX推進に不可欠な知識を紹介。設計プロセスの革新による開発期間の短縮、コスト削減、品質向上をはじめ、Azureを活用した設計DXの全貌を徹底解説しています。貴社のビジネスを成功へと導くヒントを見つけてください。
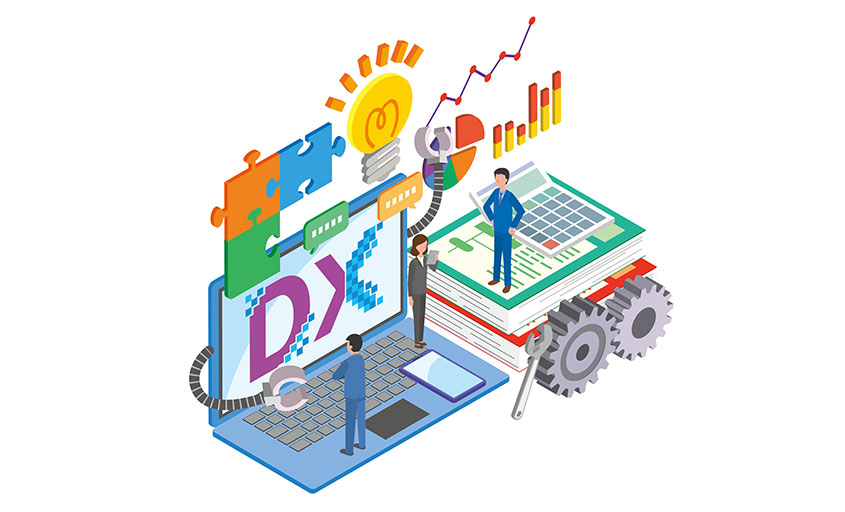
関連資料
製造業における設計DXの価値と重要性
設計DXを簡単に言い換えると、従来の設計プロセスを根本から変革することで、設計工程の効率化と高度化を実現するものです。
製造業の設計部門が直面する現代の課題
現在、製造業の設計部門は以下のような複雑かつ多岐にわたる課題に直面しています。
- グローバル競争の激化
グローバル市場での競争激化により、製品開発サイクルの大幅な短縮が求められています。同時に、コスト競争力の維持も重要な課題となっており、効率的な設計プロセスの確立が不可欠となっています。 - 技術の急速な進化
急速に進化する技術を迅速に製品に統合することが求められています。また、設計プロセス自体も継続的に刷新し、最新の技術やツールを活用して効率性と革新性を高める必要があります。 - 顧客ニーズの多様化と高度化
顧客のカスタマイズ要求が増加し、高品質と低コストの両立が求められています。さらに、顧客ニーズの変化スピードに対応するため、製品開発サイクルの短縮やバージョンアップ間隔の短縮にも柔軟に対応できる設計体制の構築が必要です。 - サステナビリティへの要求 環境負荷の少ない製品設計が求められると同時に、製品ライフサイクル全体での最適化も重要な課題となっています。設計段階から廃棄までを考慮した持続可能な製品開発が不可欠です。
- 5. 部門間連携の複雑化
設計・製造・調達など、部門をまたぐ情報共有の困難さが増しています。また、グローバルサプライチェーンの管理も複雑化しており、効率的な情報連携と意思決定のための新たな仕組みが必要とされています。
これらの課題は相互に関連し、従来の手法では効果的な対応が困難になっています。
設計DXの経営的意義
設計DXの導入は、上記の課題に対する包括的なソリューションであり、製造業にとって生き残りをかけた必須の戦略です。以下の点で企業の競争力維持・向上に貢献します。
- グローバル競争力の強化
設計DXは、製品開発プロセスを大幅に効率化し、迅速な市場投入を可能にします。これにより、急速に変化するグローバル市場での競争優位性を確保できます。同時に、デジタル技術の活用によりコスト競争力も向上し、価格面でも優位に立つことができます。 - 開発工数の削減
新技術の急速な進歩に対応するため、設計DXは開発工数の大幅な削減を実現します。AIや機械学習を活用した自動設計や、シミュレーション技術の高度化により、従来は時間と労力を要していた設計プロセスが大幅に効率化されます。これにより、エンジニアは付加価値の高い創造的な業務に集中できるようになります。 - イノベーションの加速
AIやビッグデータ分析を活用することで、従来では気づかなかった設計アプローチや製品コンセプトを創出できます。また、新技術を効率的に製品に統合することが可能となり、継続的なイノベーションを推進できます。 - サステナビリティへの貢献
設計DXは、環境負荷の少ない製品設計を可能にします。製品のライフサイクル全体をデジタル上でシミュレーションすることで、省資源・省エネルギーな設計が実現できます。これは、持続可能な社会の実現に向けた企業の責任を果たすことにもつながります。 - 顧客ニーズへの柔軟な対応
設計DXにより、カスタマイズ製品の効率的な設計と製造が可能になります。デジタルツインやパラメトリック設計の活用により、顧客の個別ニーズに応じた製品を、高品質かつ低コストで提供できるようになります。
設計DXがもたらす組織変革
部門間連携の強化
設計DXは、従来の縦割り組織の壁を取り払い、部門間の緊密な連携を可能にします。設計、製造、調達、品質管理など、異なる部門が効果的に協力することで、製品開発プロセス全体の最適化を実現します。さらに、グローバルサプライチェーンの効率的な管理も可能になり、国際的な競争力の向上につながります。
情報共有の円滑化
クラウドベースのプラットフォームを活用することで、全ての製品関連データを一元管理し、各部門がリアルタイムで情報を共有できるようになります。これにより、情報の齟齬や遅延による問題を防止し、迅速な意思決定が可能になります。結果として、製品開発のスピードが大幅に向上し、市場変化への対応力が強化されます。 このように、設計DXは単なる技術導入にとどまらず、組織全体の変革を促進します。これらの変化は、製造業の競争力を大きく向上させるだけでなく、従業員の働き方や企業文化にも前向きな影響を与え、より柔軟で革新的な組織の実現につながります。
設計DXによる市場対応力の向上
設計DXの導入は、製造業の市場対応力を大幅に向上させ、急速に変化する市場環境での競争優位性を確保します。特に以下の二つの側面で、その効果が顕著に現れます。
顧客ニーズの多様化への対応
設計DXは、多様化する顧客ニーズに柔軟に対応する力を製造業にもたらします。データ分析とAIの活用により、個々の顧客の好みや要求を正確に把握することが可能になります。これにより、カスタマイズされた製品を効率的に設計・製造することができ、大量生産から多品種少量生産へのシフトを加速させます。この変革は、顧客満足度の向上と同時に、製造業の競争力強化にもつながります。
製品ライフサイクル短縮化への対応
設計DXは、製品ライフサイクルの短縮化という課題に対する強力な解決策となります。設計から製造、販売、アフターサービスまでの全プロセスをデジタル化・一元管理することで、製品の改良や新製品の開発を迅速に実行できるようになります。これにより、市場の変化に素早く対応し、常に最新の製品を提供することが可能になります。結果として、企業は常に市場のニーズに合った製品を提供し続けることができ、競争優位性を維持することができます。
このように、設計DXは製造業の市場対応力を根本から変革し、企業の持続的な成長を支援します。
設計DXの具体的な目的と効果
これまで見てきたように、設計DXは製造業に革新的な変革をもたらします。一般的に、企業が設計DXを推進する際には、以下のような目的と期待される効果を念頭に置いています。
主な目的
- 製品開発のスピード向上
- 品質改善
- コスト削減
- 技術革新への迅速な対応
期待される具体的効果
- 開発期間の短縮
設計DXは、シミュレーションと仮想プロトタイピングを活用することで、開発プロセスを大幅に効率化します。これにより、物理的な試作品の数を削減し、開発期間を従来の半分以下に短縮することも可能になります。 - 品質向上と製品性能の最適化
高度なシミュレーション技術を用いて製品の性能や耐久性を事前に精密に予測することで、品質向上に寄与します。これにより、設計段階で潜在的な問題を特定し、製品の信頼性と性能を向上させることができます。また、製造プロセスのデジタル化により、品質管理の精度が高まり、不良品の発生を最小限に抑えることが可能になります。 - コスト削減
バーチャルプロトタイピングの導入により、材料費や試験費用を大幅に削減できます。また、設計の最適化により、製造コストの削減にもつながります。これらの取り組みにより、全体的なコスト効率が向上します。 - 顧客ニーズへの迅速な対応
データ分析とAIを活用することで、市場トレンドや顧客のフィードバックをリアルタイムで把握し、その情報を迅速に製品設計に反映できます。これにより、常に最新の顧客ニーズに応える製品を提供することが可能になります。 - 新技術の効率的な統合
デジタルツインを活用することで、新技術の検証を効率的に行うことができます。また、設計プロセス自体も継続的に最適化することで、常に最新のテクノロジーを取り入れた革新的な製品開発が可能になります。これにより、市場における技術的優位性を確保し、競争力を強化できます。
これらの効果により、設計DXは製造業の競争力を大幅に向上させ、市場での優位性を確保することができます。特に品質改善においては、顧客の声を迅速に製品に反映できるだけでなく、事前の精密なシミュレーションによって、より信頼性の高い製品を開発することが可能になります。
製造業での設計DX導入で強化・加速できること
設計DXの導入は、製造業における既存の設計プロセスや技術を大きく進化させ、その効果を飛躍的に高めます。特に以下の領域で、その影響が期待されます。
3D CADとシミュレーションによる設計プロセスの進化
3D CADとシミュレーション技術は、従来から設計プロセスの改善に貢献してきましたが、設計DXの導入によりその効果が飛躍的に向上します。2次元の図面から3Dモデルへの移行は既に進んでいましたが、設計DXはこのプロセスをさらに効率化し、部門間での3Dデータの共有と活用を促進します。
最新の3D CADツールと設計DXの統合により、製品の360度回転表示や内部構造の詳細確認が、よりスムーズかつ高速に行えるようになります。これにより、設計者の直感的な製品イメージ化や潜在的問題の早期発見がさらに容易になります。例えば、部品の干渉チェックは、設計DXによってリアルタイムで自動的に行われ、即座にフィードバックを得ることができます。
シミュレーション技術の統合による効果の増大
3D CADとシミュレーション技術の組み合わせは以前から行われていましたが、設計DXの導入により、その効果が大幅に向上します。クラウドコンピューティングやAIの活用により、強度解析、熱解析、流体解析などのシミュレーションがより高速かつ高精度で実行可能になります。これにより、試作品製作前の製品挙動予測の精度が向上し、開発コストと時間の削減効果がさらに増大します。
バーチャルプロトタイピングの高度化
バーチャルプロトタイピングは既存の技術ですが、設計DXの導入によりその効果と適用範囲が大きく拡大します。例えば、自動車業界での衝突シミュレーションは、設計DXによってより複雑な条件下でのテストが可能になり、実車での破壊試験回数をさらに減らすことができます。また、AIを活用した予測モデルにより、シミュレーション精度が向上し、コスト削減と開発期間短縮の効果が一層高まります。
さらに、設計DXは、これらの技術をより統合的に活用することを可能にします。3D CAD、シミュレーション、バーチャルプロトタイピングのデータを一元管理し、部門間で即時に共有することで、設計プロセス全体の効率が飛躍的に向上します。これにより、製品開発サイクルの大幅な短縮と、より革新的な製品設計の実現が可能となるのです。
関連資料
デジタルツインを活用した設計と生産の連携
デジタルツイン技術は、物理的な製品とそのデジタル表現をリアルタイムで同期させる革新的な手法です。設計と生産のギャップを埋めることで、設計から生産までという、製品ライフサイクルのより広い範囲の最適化ができます。また、実際の物理的な製品を作る前にデジタル空間で実際の製品シミュレーションができるので、設計や生産に関わる迅速な意思決定も可能になります。
デジタルツイン技術の基本概念
デジタルツインは、現実の製品やプロセスの仮想コピーです。センサーからのデータをリアルタイムで反映し、製品の状態や性能をモニタリングします。例えば、工作機械のデジタルツインを作成すれば、その稼働状況や摩耗状態をリアルタイムで把握できるのです。
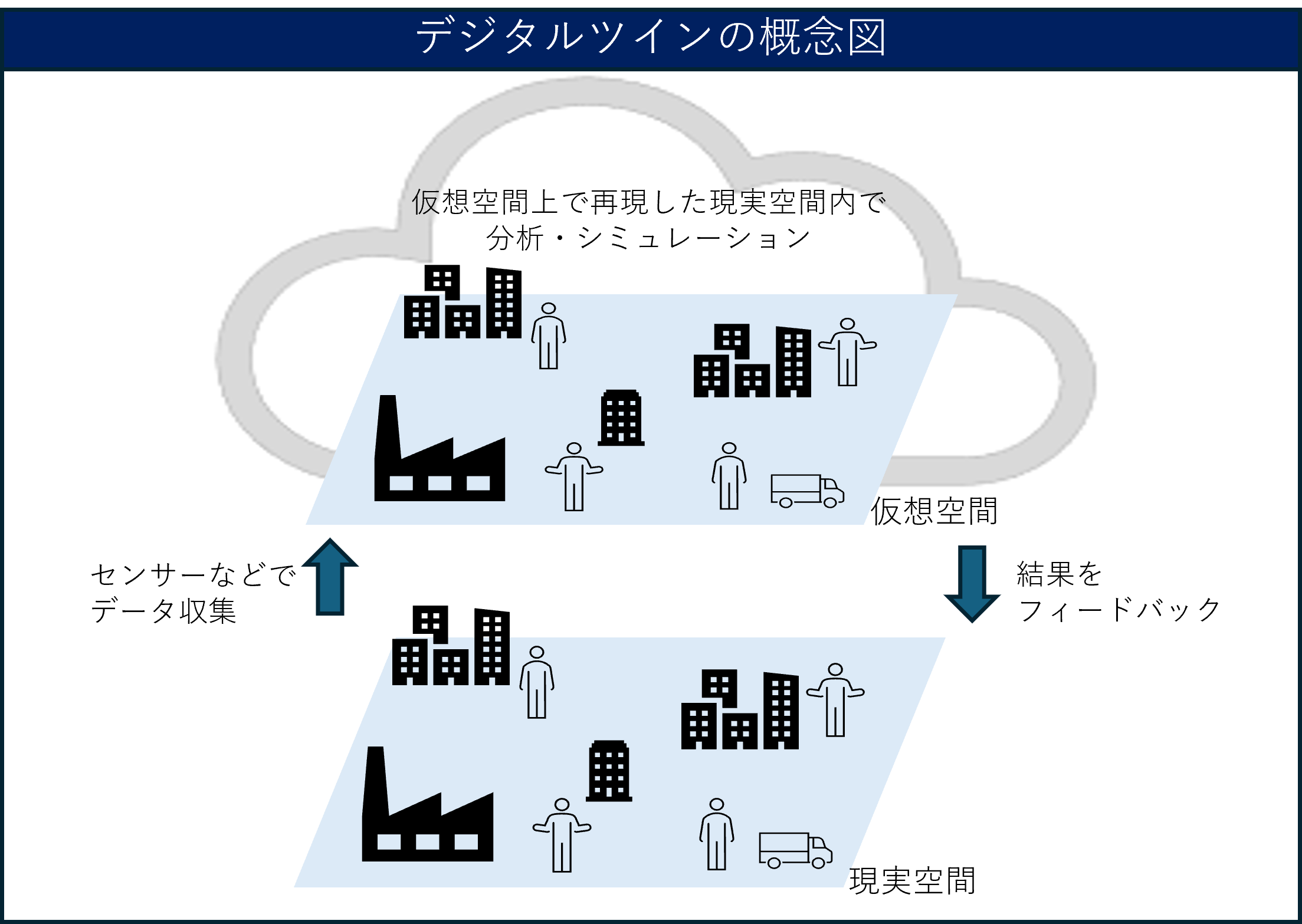
設計段階でのデジタルツイン活用
設計段階でデジタルツインを活用すれば、製品の性能や耐久性を事前に予測できます。例えば、航空機エンジンの設計では、さまざまな飛行条件下での性能をシミュレーションし、最適な設計を見出すことができます。これにより、開発リスクを低減し、より信頼性の高い製品を生み出せるのです。
生産プロセスとの連携によるメリット
デジタルツインを生産プロセスと連携させることで、設計の変更が製造にどのような影響を与えるかを即座に確認できます。例えば、ある部品の設計を変更した場合、その変更が組立ラインの効率にどう影響するかをシミュレーションできます。これにより、設計と製造のギャップを埋め、より効率的な生産システムを構築できるのです。
サステナビリティを考慮した設計DXの重要性
設計や生産プロセスの短縮と並び、製造業の設計部門が直面する現代の課題の一つとして、サステナビリティ対応も忘れてはなりません。環境への配慮は、これからの設計DXにおいて最も重要なテーマの一つとなるでしょう。
ライフサイクルアセスメントの設計DXへの統合
製品の設計段階から、原材料の調達、製造、使用、廃棄までの全ライフサイクルにおける環境影響を評価し、最小化する取り組みが進むでしょう。AIを活用して、環境負荷と性能、コストのバランスを最適化する設計手法が一般的になるかもしれません。
循環経済を促進する設計アプローチ
製品の長寿命化、修理のしやすさ、リサイクル性の向上など、循環経済を前提とした設計が求められるようになるでしょう。例えば、使用済み製品の解体・リサイクルプロセスまでを考慮した「逆設計」のような概念が重要になるかもしれません。
エネルギー効率を最適化する設計手法の発展
製品自体の省エネ性能向上はもちろん、製造プロセスのエネルギー効率も含めた総合的な最適化が求められるようになるでしょう。AIとシミュレーション技術を駆使して、製品のライフサイクル全体でのエネルギー消費を最小化する設計手法が発展していくことでしょう。
設計DXの導入ステップ
ここからは設計DXの導入について説明していきます。
設計DXの導入は、単なるツールの導入ではなく、組織全体の変革を伴う大規模なプロジェクトです。成功するためには、以下の段階を慎重に進める必要があります。

現状分析とゴール設定
まず、現在の設計プロセスの詳細な分析を行います。ボトルネックや非効率な部分を特定し、設計DX導入後のあるべき姿を明確にします。例えば、「設計期間を30%短縮」「設計変更の回数を50%削減」といった具体的な数値目標を設定します。
戦略立案
目標達成のための包括的な戦略を立案します。これには、必要な技術の選定、人材育成計画、組織構造の再設計などが含まれます。また、段階的な導入計画や、パイロットプロジェクトの選定なども行います。
実行計画の策定
戦略を具体的なアクションプランに落とし込みます。各施策の優先順位付け、必要なリソースの割り当て、タイムラインの設定などを行います。また、リスク管理計画や変更管理計画も策定します。
技術選定と導入
設計DXに必要な技術やツールを選定し、導入します。3D CADやシミュレーションソフトウェア、PLMシステム、クラウドプラットフォームなどが含まれます。導入にあたっては、ユーザートレーニングや既存データの移行なども並行して行います。
各段階での具体的なアプローチや注意点については、「DX時代に求められる業務効率化とその方法とは?」をご覧ください。
設計DXを支える技術やツール
設計DXの実現には、支える技術やツールの導入・活用が不可欠です。代表的なものを以下に挙げます。
PLM(製品ライフサイクル管理、Product Lifecycle Management)
PLMは、製品の企画から設計、製造、販売、保守までの全ライフサイクルを一元管理するシステムです。設計DXにおいて、PLMは以下の役割を果たします。
- データの一元管理:設計データ、製造情報、顧客フィードバックなどを統合管理
- バージョン管理:設計変更の履歴を追跡し、最新版を常に把握
- コラボレーション促進:部門間や取引先との情報共有を円滑化
- トレーサビリティの確保:製品の設計から廃棄までの全過程を追跡可能
PLMについては、「PLMって何?AI時代の製造業に必須の製品ライフサイクル管理を徹底解説」もご覧ください。
CAE(Computer Aided Engineering)
CAEは、コンピュータ上で製品の性能や耐久性をシミュレーションする技術です。設計DXにおけるCAEの主な用途は以下です。
- 構造解析:製品の強度や耐久性を予測
- 熱解析:熱伝導や冷却効果をシミュレーション
- 流体解析:流体の挙動や空気抵抗を計算
- 電磁界解析:電子機器の性能を予測
CAEの活用により、物理的な試作品の数を大幅に削減し、開発期間の短縮とコスト削減を実現できます。
HPC(High Performance Computing)
HPCは、大規模な計算処理を高速で行うコンピューティング環境です。大規模なデータを扱うことが多い設計DXにおけるHPCの主な役割は以下です。
- 複雑なシミュレーションの高速処理
- ビッグデータ解析による設計最適化
- AI・機械学習モデルの学習と推論の高速化
これらの技術やツールを効果的に組み合わせることで、設計DXの真価を発揮することができます。例えば、PLMで管理された設計データをCAEで解析し、その結果をHPCで高速処理することで、製品の設計性能を迅速に最適化できます。
クラウドテクノロジーとAIの設計DXへの活用
AIとクラウド技術の融合は、設計プロセスに新たな可能性をもたらしています。地理的な制約を超えた協働が可能になり、より創造的で効率的な設計が実現できるのです。
クラウドベースの設計環境
クラウドベースの設計環境は、従来のオンプレミス環境の制約を解消し、柔軟で拡張性の高い設計プラットフォームを提供します。この環境では、高性能な計算リソースへのアクセス、大容量のデータストレージ、そしてグローバルな協働が可能になります。
クラウドを活用した大規模計算と協調設計
クラウドコンピューティングの活用により、膨大な計算リソースを必要とするシミュレーションや最適化計算を、短時間で実行できるようになりました。例えば、自動車の空力解析では、数百のケースを並行して計算することで、最適な車体形状を迅速に見出すことができます。
グローバル協業を可能にするデータ共有
クラウドベースの設計環境により、世界中の設計者が同じデータにアクセスし、リアルタイムで協働できるようになりました。例えば、日本の設計チームが作業を終えた後、欧州のチームがそれを引き継ぎ、さらに北米のチームへとバトンを渡すことで、24時間365日ノンストップの開発が可能になるのです。
このように、設計DXは製造業に革新的な変革をもたらしています。従来の設計プロセスの限界を超え、より効率的で創造的な製品開発を実現することで、企業の競争力を大きく向上させることができるのです。
AI・機械学習による設計最適化
AIは設計プロセスに革命をもたらし、人間の創造性を拡張し、従来では考えられなかった革新的な設計解を生み出します。AI技術は、大量のデータから学習し、複雑な設計要件を満たす最適解を高速に探索することができます。
設計者が要求事項と制約条件を入力すると、AIが数千、数万もの設計案を生成します。また、機械学習を用いた設計最適化は、大量のデータから学習したAIモデルを活用して、設計プロセスを効率化し、最適な設計案を導き出す手法です。
例えば、航空機の部品設計では強度と軽量化の両立が求められますが、AIはこの相反する要求を満たす革新的な形状の提案を出してくれたりします。また、機械学習データをもとに、複雑な設計パラメータの組み合わせを高速に探索し、人間の直感では気づきにくい最適解を見つけ出すこといったことも可能になります。
AIとクラウドの統合による協調設計の実現
AIとクラウド技術の統合は、設計プロセスに革新をもたらし、グローバルな協調設計を可能にします。この統合により、地理的に分散したチームが効率的に協力し、リアルタイムでデータを共有しながら、AIの支援を受けて設計を進めることができます。
リアルタイムコラボレーションツール
クラウドベースのリアルタイムコラボレーションツールは、設計チーム間のシームレスな情報共有と協力を実現します。例えば、3D CADモデルをクラウド上で共有し、複数の設計者が同時に編集やレビューを行うことができます。これにより、設計の進捗が加速し、チーム間のコミュニケーションが大幅に改善されます。
AIとクラウドを活用した設計プロセスの自動化
AIとクラウドの組み合わせにより、設計プロセスの多くの部分を自動化することが可能になります。例えば、設計パラメータの最適化、設計案の自動生成、シミュレーション結果の分析などをAIが行い、その結果をクラウド上で即座に共有することができます。これにより、設計者は創造的な作業により多くの時間を割くことができるようになります。
“AI×クラウド”を駆使した設計開発業務のDXを実現するAzure HPCとAzure CycleCloud
先に挙げた、「PLMで管理された設計データをCAEで解析し、その解析をHPCで高速処理することで、製品の設計性能を迅速に最適化するといったユースケース」をクラウド上で実現するためには、Azureのハイパフォーマンスコンピューティング環境を提供するAzure HPCが最適です。高性能コンピューティング(HPC)ワークロードを効率的に実行するためのサービスです。
また、Azure 上の HPC環境を展開・管理するために、Azure CycleCloud というツールが提供されています。
詳しくは、「DXで実現する設計開発業務のイノベーションシナリオ」をご参照ください。
設計DX導入における課題
これまで説明してきたとおり、設計DXの導入には多くのメリットがあり、また、設計DX導入を容易にするサービスがありますが、他にいくつかの課題もあります。
既存システムとの統合
多くの企業では、長年使用してきた設計システムやデータベースが存在します。これらのレガシーシステムと設計DXのシステムをいかにシームレスに統合するかが大きな課題となります。この問題に対しては、段階的な移行計画を立て、APIやミドルウェア最新のクラウドサービスやAPIなどの連携技術を活用した柔軟な統合アプローチが効果的です。
既存システムとの統合
多くの企業では、長年使用してきた設計システムやデータベースが存在します。これらのレガシーシステムと設計DXのシステムをいかにシームレスに統合するかが大きな課題となります。この問題に対しては、段階的な移行計画を立て、APIやミドルウェア最新のクラウドサービスやAPIなどの連携技術を活用した柔軟な統合アプローチが効果的です。
セキュリティ対策
設計DXでは、クラウド上で大量の機密データを扱うため、セキュリティの確保が極めて重要です。データの暗号化、アクセス制御、定期的なセキュリティ監査など、包括的なセキュリティ対策が必要となります。また、サプライチェーン全体でのセキュリティ意識の向上も欠かせません。
なお、工場設備で使われるIoTデバイスなどのセキュリティについては、「攻撃に負けない工場を作る ~製造業のためのサイバーセキュリティ対策指南書~」や、「OTのセキュリティは大丈夫?知っておくべき脅威と工場現場を強固に守るための対策」を参照してください。
人材育成と組織の変革
設計DXの導入には、新しいスキルセットを持つ人材が必要です。3D CADやシミュレーションツールの操作はもちろん、データ分析やAIの基礎知識も求められます。この課題に対しては、社内研修プログラムの充実や、外部の専門家との連携が有効です。また、場合によっては、従来の縦割り組織から、より柔軟でアジャイルな組織への転換も重要です。
関連資料
設計DX導入を包括的に支援する東京エレクトロンデバイス
東京エレクトロンデバイスは、Azure CSPライセンス、Azure HPCやAzure CycleCloud、他のAzureサービスの導入支援まで、豊富な経験と知見を持つ専門家チームやパートナー企業により、貴社の設計DX導入を包括的に支援します。
設計DXの将来展望
設計DXは、AIとビッグデータの活用・進化に伴って、ますます発展していくことが予想されます。設計プロセスはより効率的に、より創造的になっていくことでしょう。
自律的設計最適化の可能性
近い将来、AIが人間の設計者と協調しながら、自律的に設計の最適化を行う時代が来るかもしれません。例えば、変化する制約条件を認識しながら、製品の性能、コスト、製造キャパシティなどをその時の状態に応じて自律的に最適化するといったものです。
自然言語処理を活用した設計要求の自動解釈
自然言語処理技術の進化により、顧客ニーズや市場のトレンドを自動的に解析し、設計に反映させることが可能になるでしょう。SNSやレビューサイトの分析から、次世代製品の仕様を自動的に提案するシステムも夢ではありません。
AIによる創造的設計提案の実現
AIが人間の創造性を補完し、まったく新しい設計コンセプトを提案する日も近いかもしれません。例えば、生物の進化をモデルにした「エボリューショナリー・デザイン」など、人間の発想を超えた革新的な設計手法の実現が期待されています。
設計DXが切り拓く製造業の未来
設計DXは製造業に革命的な変化をもたらし、その進化は今後も続いていきます。設計DXの導入は、もはや選択肢ではなく、必須の戦略なのです。
設計DXは今日の明日で実現できるものではありません。東京エレクトロンデバイスと一緒に貴社の設計DXを検討してみませんか?
設計DXに関するFAQ
Q.設計DXと従来の設計プロセスの主な違いは何ですか?
データとデジタル技術の全面活用、リアルタイムな情報共有、高度なシミュレーション能力が主な違いです。
Q.中小製造業でも設計DXは導入可能ですか?
可能です。クラウドサービスの活用や段階的な導入で、初期投資を抑えつつ効果を得られます。当社のAzure CSPライセンスは、中小企業様にも柔軟に対応できるソリューションです。
Q.設計DXのROIはどのように測定しますか?
開発期間短縮率、コスト削減額、品質向上度、売上増加率など、複数の指標を総合的に評価します。
Q.設計DXにおいて最も重要なスキルセットは何ですか?
3D CAD操作、データ分析、AI基礎知識、クラウド技術の理解が重要で、継続的な学習も必要です。東京エレクトロンデバイスは、Azure CSPライセンス販売とAzure導入支援を通じて、お客様の設計DXをトータルにサポートします。最適なAzureソリューションの設計と実装をお手伝いいたします。